Project Overview
The SUEZ Recycling Facility project is a state-of-the-art £27m development in Aberdeen, designed to help the community reduce its environmental impact. Our team played a key role in delivering this ambitious project through a comprehensive scope of works. A fire tragically destroyed the original building in 2022, so the goal was to rebuild it in a way that blended seamlessly with the remaining structure. Additionally, the renovations needed to provide enhanced durability, fire resistance and energy efficiency.
Scope of Work
Working to main contractor, Morrison Construction, KR Group fabricated and installed the structural steel, and installed roof and wall cladding, alongside internal fire walls. Our roofing work on this project, included safety aspects such as edge restraints and safety netting. Spanning an impressive 144m in length and 77m in width, the roof was a major element of the build.
Materials
KR Group fabricated and installed structural steel to reconstruct damaged sections of the building frame.
Our team then constructed the roof using Kingspan 40mm QuadCore KS100RW roof panels. These panels are through-fix, profiled insulated panels ideal for roof pitches of 4° or more after deflection. These panels are 1000mm wide and, due to their prefabricated nature, allowed for faster installation compared to traditional roofing methods.
This approach ensured the roof was wind- and water-tight almost immediately, reducing construction risks and project timelines.
The cladding combined five colours of Kingspan KS1000RW “Trapezoidal” panels with Kingspan XL Forte composite panels, blending the building into its surroundings. Our team integrated Brett Martin Safelight Energy Saver trapezoidal GRP rooflights into the roof to enhance energy efficiency. Internally, fire walls were specified and installed in line with requirements, using Tata Trinsul vertically laid firewalls with 150mm deep profiled rock fibre slabs.
Challenges and highlights
The project team faced a major challenge: they had to recreate the original building, which a fire destroyed in 2022, while simultaneously upgrading it to meet higher quality specifications. This task required careful consideration to ensure the new structure not only met current building standards but also preserved the visual essence and character of the original design.
The process involved numerous design meetings and consultations between stakeholders, including architects, engineers, and product manufacturers. Ultimately, the collaborative effort ensured that the final structure paid homage to its predecessor while offering enhanced safety and functionality for the future.
Additionally, due to fire damage, there was a complex approval process involving the client, contractor and client’s insurance company and loss adjuster. Our team coordinated closely to process every change efficiently and keep the project on track. Flexibility was critical, and our team excelled in adapting to these evolving requirements while maintaining focus on quality and deadlines.
Safety, quality, and compliance
As a UKAS ISO 9001, 14001, and 45001-accredited contractor, we deliver our projects to the highest standards of quality, environmental responsibility, health, safety, and structural integrity. Our comprehensive library of policies and procedures supports these accreditations, embedding health, safety, environmental and quality at every project stage—from design to material procurement via a local and sustainable supply chain, to implementing safe practices, waste management, and CO? reduction aligned with the UN Sustainable Development Goals.
On this, and all other projects, we conduct regular site inspections to proactively address potential issues, working closely with suppliers to phase deliveries, keeping project sites tidy and minimising material loss or damage.
Built to the architect and engineers’ specifications, the project included essential safety and maintenance features, incorporated during construction. Our director, CAD team, and Operations Manager carefully programmed each phase of the work to execute it safely, efficiently, and with minimal environmental impact.
Our team utilised on-site iPads to reduce paper usage, access real-time drawings, and save time while supporting sustainability. They also segregated waste, and stored in line with our Waste Policy, maximising reuse, recycling, and circular initiatives. We collaborated with supply chains offering waste collection and optimised logistics to reduce fuel consumption and emissions.
Client feedback
As part of the project, we installed safety netting and edge protection to FASET (Fall Arrest Safety Equipment Training) standards. FASET recognised our efforts when our Temporary Works Supervisor won Installer of the Year for his leadership on the project.
Our client highlighted the professionalism and quality of our work:
“They demonstrated exceptional knowledge of RAMS and executed the installation safely and efficiently. Their innovative approach and ability to assist with a varied scope of operations made them a trusted partner. With KR Group, we felt confident that work was being carried out to the highest standards, relieving pressure on our team.”
Our team’s dedication to excellence and proactive approach exceeded client expectations. The principal contractor praised us for our professionalism, flexibility, and ability to “think on our feet”. As a team, we tackled every challenge without compromising on quality or timelines. By overcoming hurdles with expertise and precision, we successfully delivered a project that met budget and client satisfaction.
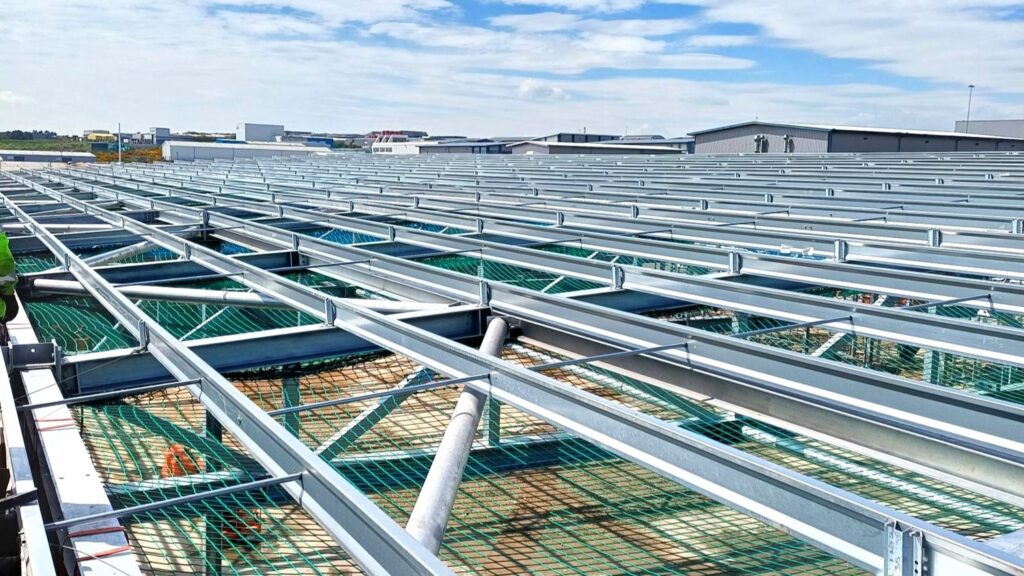
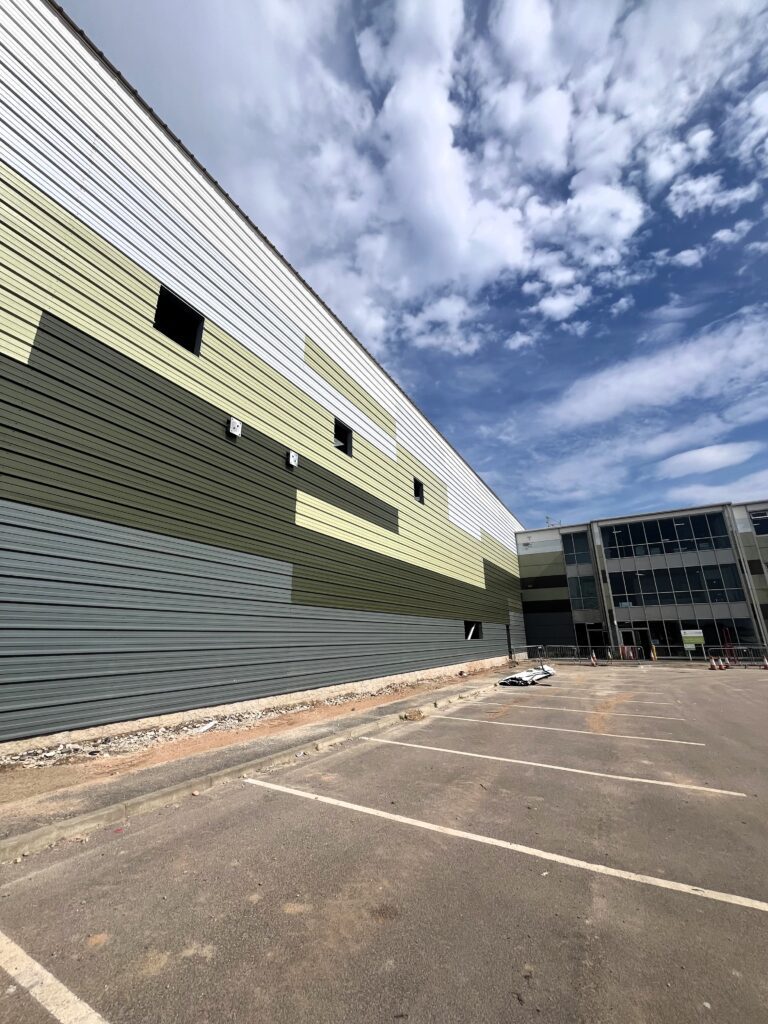
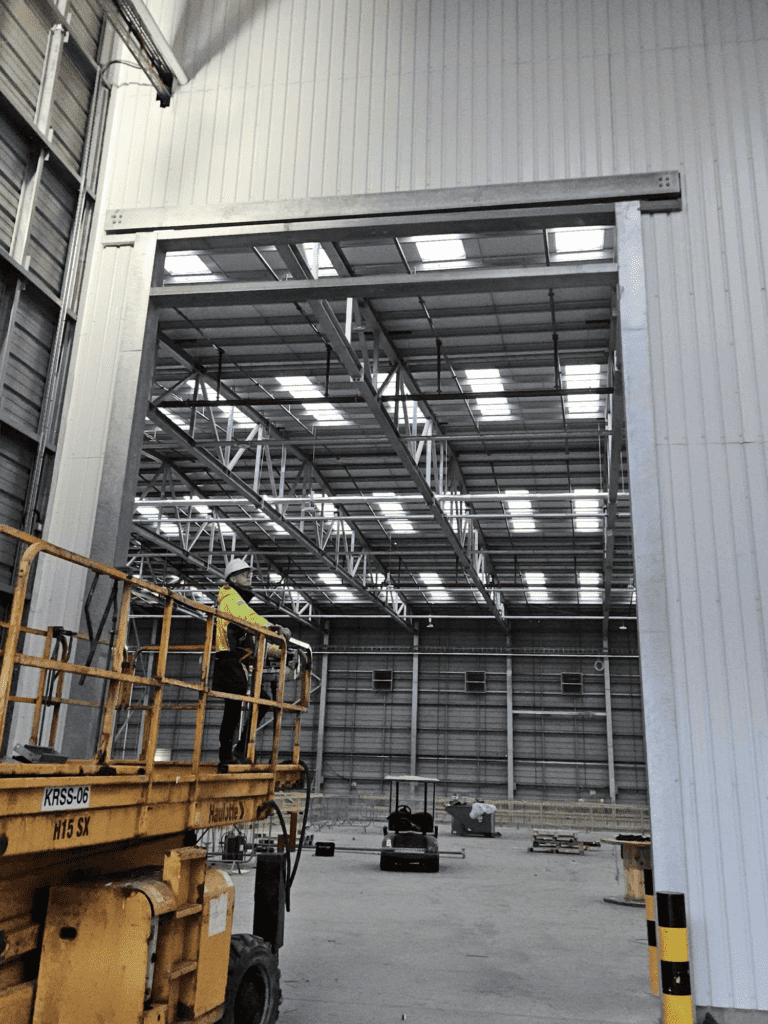
Need a steel, cladding and sheet metal contractor for your next project? Contact our responsive team via info@krgrp.co.uk. For more examples of what we can do, visit our Projects page.